Cost management is important in capital projects of all sizes, but generally, the larger the project, the higher the risk for going over budget or beyond the estimated completion timeline. A project owner must be able to avoid schedule creep, change orders, and inaccurate reporting in order to maximize the delivered value. From front-end engineering to on-site construction, transparency and communication are crucial in establishing cost management strategies.
Typically, capital project cost management is broken down into four stages—resource planning, cost estimation, cost budgeting, and cost control. Each of these stages plays an essential role in ensuring the success of a project.
Let’s dive deeper into effective cost management strategies and how using an EPC (engineering, construction, and procurement) approach can maximize cost planning and control.
Capital Cost Management Processes
Having the right tools and procedures in place can prevent cost overruns and ensure the successful execution of a capital project. Each stage of the capital project cost management process is detailed below.
Resource Planning
It’s essential to develop and define a strong project scope during front-end planning to ensure a capital project remains on schedule and within budget with as few change orders as possible during project execution. Before any work can begin, the resources required to complete the project must first be established. This is known as resource planning.
During resource planning, the materials and equipment that are needed to complete the project are identified. Labor is also included in resource planning. To simplify the process, a Work Breakdown Structure (WBS) is often utilized. A WBS is a visual diagram used for organizing tasks and deliverables and breaking them down into smaller components to make project execution more manageable. This approach enables project owners to produce an accurate inventory of everything that’s needed during the capital project life cycle.
Cost Estimation
After all of the required resources have been identified, they will need to be priced to establish a total cost estimate. This should not be a one-time process—to ensure effective cost management, cost estimations will need to be reevaluated based on changes to the scope throughout the project. An analogous estimation, which is a technique that uses information from similar or previously completed projects, can be used to obtain a rough cost approximation.
To establish a cost estimate that’s as accurate as possible, the following information should be considered:
- The price of each required resource (e.g. labor, material, and fabrication costs)
- The quantity and duration of each required resource
- Potential risks such as change orders and schedule overruns
Initially, cost estimates are usually a Rough Order of Magnitude at +/- 50%. These estimates should become more accurate and defined as the project progresses through the front-end planning, detail design, and construction stages.
Cost Budgeting
Once the initial cost estimation process has been completed, the project budget can then be developed. Information from the resource planning process, such as the data contained in the WBS, as well as from the cost estimation process, is used to determine a cost baseline. A buffer should always be included in the budget to account for any change orders or cost overruns that might occur throughout the project.
Cost Control
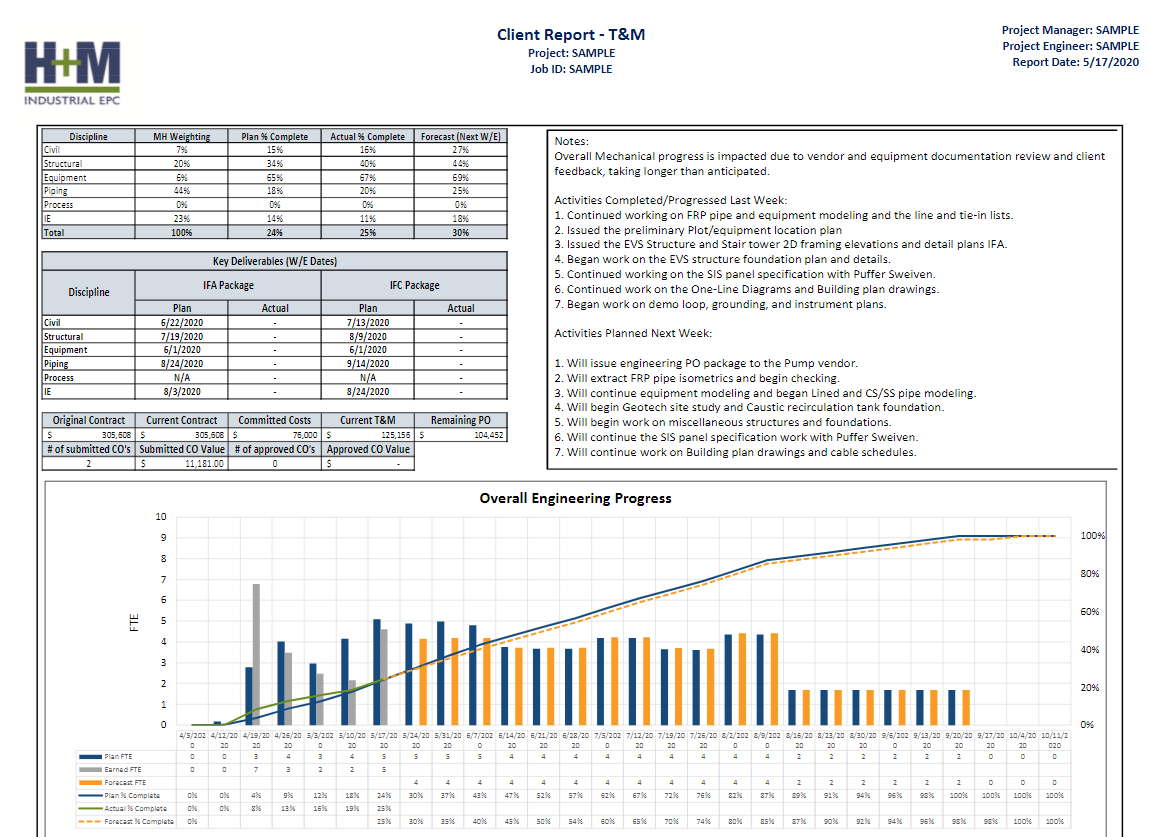
To prevent scope creep and ensure that a capital project remains on budget, it’s important to employ effective cost control measures such as project reporting. This is a continuous process that is performed throughout the entirety of the project.
The following project controls are often used by owners and contractors to control costs in capital projects:
- Earned value management: This is a project management technique that objectively measures the progress and performance of a project against the project’s WBS, schedule, and budget. Variances between earned value, planned value, and actual value can be depicted using S-curve plots on a graph known as an earned value analysis. This allows the project owner to easily visualize any differences between the estimated cost and the actual cost of the project.
- Contractor project reports: To ensure that any deviations from the budget and schedule plans are addressed quickly and efficiently, contractors should routinely provide progress reports to the project owner. These reports should contain important information such as progress and performance measurements, cost reports and breakdowns, and daily headcounts.
- Change management procedures: Having effective change management procedures in place can help mitigate the cost damages that project scope changes can cause. In addition to providing detailed change order requests with information including the requestor’s name, a thorough description of the requested change, schedule impact, and total cost and hours by discipline, regular meetings should also be established between the contractor and the project owner. Workflows and procedures for implementing any changes should also be developed.
How EPC Can Maximize Cost Planning and Control
Depending on project objectives, utilizing the EPC project delivery approach can benefit project owners who have a variety of requirements they wish to achieve. In this method, project risk is transferred from the owner to the EPC contractor, who will have experience in integrating design, engineering, procurement, and construction teams. This integration can often allow for project stage overlap, which enables projects to be completed faster with a high level of quality. By being able to execute projects more quickly, project owners can save on labor and schedule costs.
In addition to the transfer of risk, the owner can also minimize their management resources and take a more hands-off approach to the project. Many EPC contractors also have in-house procurement and fabrication teams, which can help with vendor and subcontractor costs.
The H+M Approach to Capital Project Cost Management
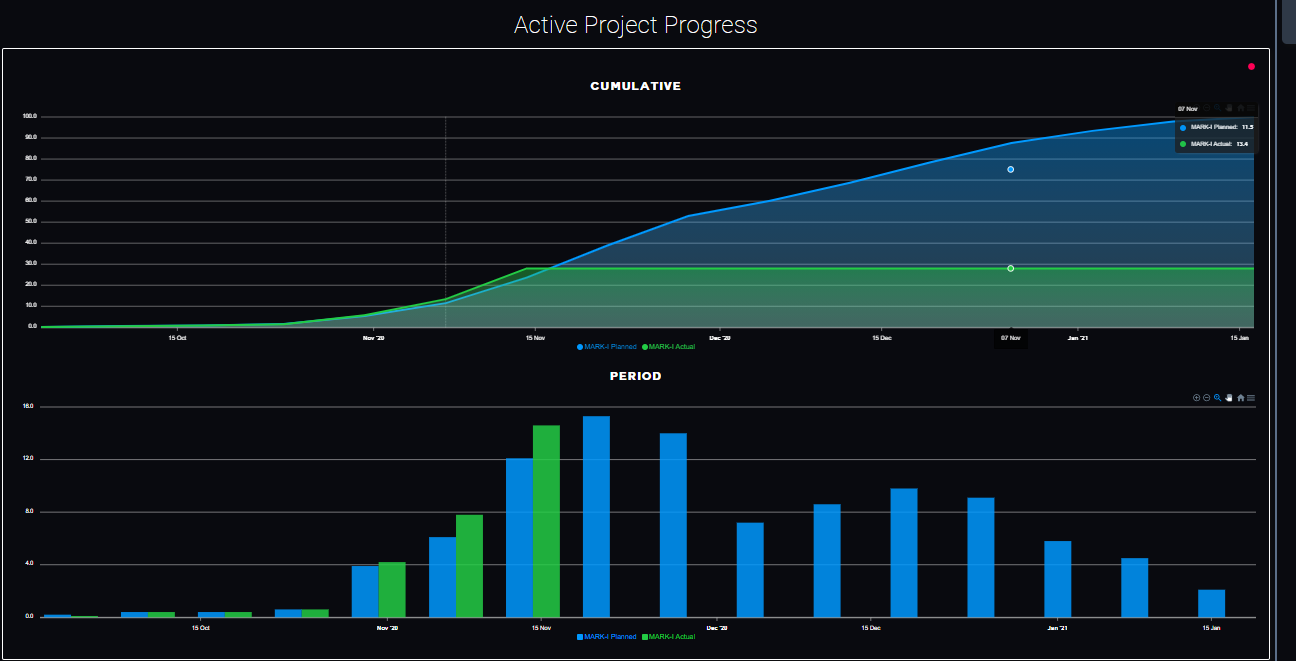
At H+M Industrial EPC, we use our integrated approach and capital project cost management best practices to execute your project on time and within budget. We know how important timely communication is to the success of a project, and we work with you to ensure your plan is followed from start to finish.

The H+M Industrial Team
For over three decades, we have provided best-in-class capital project management services to Energy and Chemical industries through our proven EPC approach. We are dedicated to providing trust, experience, and efficiency through all stages of engineering, procurement, and construction--on budget and on time.
Partnering with H+M Modular
H+M Modular, a division of H+M Industrial EPC, specializes in custom fabricated equipment, modules, and skids for energy and chemical industries. The approach emphasizes the potential for decreased risk through more controlled fabrication, leading to enhanced quality and safety, reduced labor costs and construction times, improved labor availability, and solutions to geographic challenges. We are dedicated to providing trust, experience, and efficiency through all stages of traditional and modular construction projects using our proven EPFC approach, If you're considering modular fabrication, we invite you to connect with us to learn about how modular solutions can improve project outcomes.