Capital projects are complex and contain many moving parts that can introduce project risk and uncertainty, potentially impacting costs. Project risk is an uncertain condition or event affecting many project objectives, including scope, cost, schedule, and quality. Therefore, contractors must assess project risks not only to inform risk management planning and procedures but cost estimates as well.
The development and analysis of detailed construction risk profiles help contractors establish accurate cost estimates. When developing cost estimates, risk factors such as schedule, location, and safety concerns should be considered, analyzed, and implemented when developing cost estimates.
Let’s take a deeper look into risk factors to consider when developing a construction risk profile and how risk profiles affect cost estimates.
Risks To Consider When Developing Construction Risk Profiles
When developing construction risk profiles, there are several important risk factors to consider. Factors include schedule, location, safety concerns, the use of subcontractors, and material supply availability, and financial aspects such as liquidated damages, performance bonding, and the financial strength of the project owner. Analyzing each risk profile allows contractors to understand the risks they are taking on to apply proper contingencies for each aspect of the project.
Schedule
Requested or required completion dates are one of the most significant driving factors for the cost of a project. Tight project timelines often require additional resources and labor, such as needing more personnel or equipment. Contractors often run into requested schedules that are shorter than what is realistically achievable. This type of risk must then be priced into the project costs for the contractor to utilize the necessary resources to make the job achievable.
Location
Depending on the site location and the source of equipment and materials, there may be risks surrounding the cost of site mobilization in addition to freight costs. Weather and unexpected site conditions are often the culprits of unforeseen project delays. For example, if a job requires a lot of excavation or trench work at a site located in an area like South Texas during the rainy season, this is a risk factor that should be considered when estimating project costs.
Safety Concerns
Safety concerns, such as performing extra hazardous work on an active or operating facility, should be considered when developing construction risk profiles and cost estimates. Before signing a contract, the following should be considered:
- Their working history of the contractor with the project owner.
- The project contractor and owner’s work and safety culture.
Both the owner and contractor must hold safety as the highest priority and have work processes that integrate safety into operational tasks to effectively mitigate safety risk.
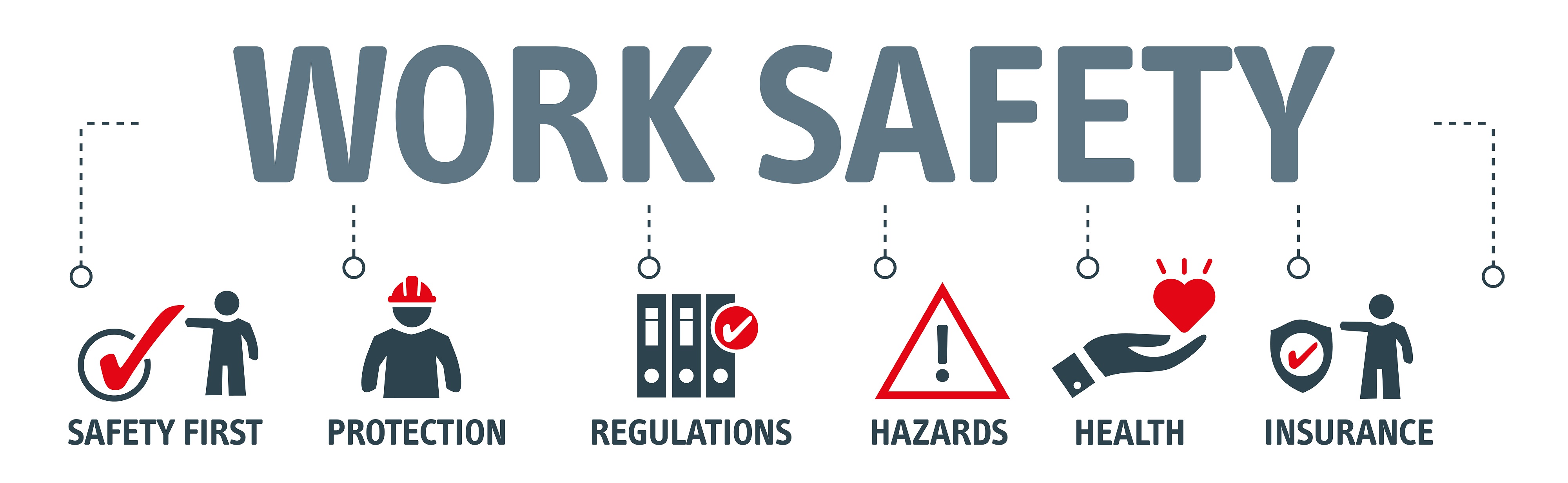
Use of Subcontractors
When utilizing discipline-specific subcontractors, it is essential to ensure that subcontractors capture the full scope of what is required of them and that they have not left out scope unintentionally or qualified out any scope. If they have, the primary contractor may be required to pick up the cost, and the uncertainty may ultimately lead to price increases. In addition, the history of the subcontractor in regards to how they treat safety culture and handle management, invoicing, and accounting may also play a role in the development of cost estimates.
Material Supply Availability
It is challenging to predict future market conditions and material supply availability. When owners ask for price holds for extended periods, contractors have no certainty regarding what will happen in the market. To accommodate requests like this, the only option contractors have to mitigate risks is to add contingency. During project execution, it’s important to try to purchase equipment and materials early on or lock in the price of the equipment. Material and equipment lead times can drive the project schedule and consequently drive project completion. Contractors and owners need to know how much lead time is necessary to buy the equipment and materials upfront, as this allows the schedule to be built around that.
Liquidated Damages
When owners require liquidated damage in a project, the risk is closely tied to the schedule, as the project must finish mechanical completion by a fixed date. While most organizations have a cap at 5-10% of project costs, this places massive risk on the contractor, particularly with larger, more expensive projects. What's not always understood is that when liquidated damage is required, the full risk is included in the cost estimate. While contractors can control their schedule and do what is needed to meet deadlines, there are often specific touchpoints the client has to respond to that can impact their ability to achieve mechanical completion by the fixed date. For example, if the owner doesn’t give the contractor drawings, purchase specific equipment and materials, or provide site access, the mechanical completion date may not feasibly be able to be met.
Performance Bonding
In some cases, project owners may require performance bonding to 100% of the project, which increases the cost of the project significantly, as the cost of the bond itself is fixed. This creates a risk for the contractor because each organization has a financial limit for the number of bonds they can carry at any point in time. This can consequently cap the number of projects the contractor can begin. For this reason, contractors must build this into the cost of the project.
Financial Strength of Project Owner
A project owner’s payment schedule and history may be included in the development of construction risk profiles and cost estimates. For example, if a project owner insists on pushing out payment terms as far as possible, the contractor is essentially financing the project, which impacts their organization’s working capital. The slower the owner pays the contractor, the more the contractor has to borrow from the bank to fund the project. This can potentially lead contractors to reach their cap for the number of projects they can take on.
How Risk Profiles Affect Cost Estimates
After risk identification, each risk component is analyzed separately to determine whether or not there is an appropriate mitigating factor. Risks can then be ranked through both quantitative and qualitative analysis while determining ballpark estimates for potential cost impacts of each risk component. Based on this analysis and the likelihood of each risk, contractors assign appropriate contingencies for each risk to inform cost estimates.
Typically, schedule variability is the most significant risk factor that drives cost estimations due to the cost of indirect personnel and indirect equipment and materials. The incremental cost for each day the project duration stretches is substantial. Unrealistic schedule requests place significant risk on contractors, which often needs to be built into project costs.
The H+M Approach to Risk Profile and Cost Estimate Development
At H+M Industrial, we are dedicated to doing everything we can to execute your project successfully—on budget and on time. Whether you have strict schedule restraints or other driving factors, we do everything we can to make it achievable. Our cost estimating team has more than 100 years of combined experience, allowing us to provide you with a competitive yet realistic project cost estimate. We work tirelessly to identify risks as early as possible and develop the most strategic mitigation strategies to drive project success.

The H+M Industrial Team
For over three decades, we have provided best-in-class capital project management services to Energy and Chemical industries through our proven EPC approach. We are dedicated to providing trust, experience, and efficiency through all stages of engineering, procurement, and construction--on budget and on time.
Partnering with H+M Modular
H+M Modular, a division of H+M Industrial EPC, specializes in custom fabricated equipment, modules, and skids for energy and chemical industries. The approach emphasizes the potential for decreased risk through more controlled fabrication, leading to enhanced quality and safety, reduced labor costs and construction times, improved labor availability, and solutions to geographic challenges. We are dedicated to providing trust, experience, and efficiency through all stages of traditional and modular construction projects using our proven EPFC approach, If you're considering modular fabrication, we invite you to connect with us to learn about how modular solutions can improve project outcomes.