From the planning phases of industrial construction projects through project execution, it is essential to exchange information and collaborate within engineering disciplines. The documents used to convey engineering information and foster continuity across disciplines are called deliverables.
In this article, we provide a list of common process engineering deliverables for capital projects.
Process Engineering Deliverables List
Every capital project is unique—consequently, process engineering deliverables produced throughout the project lifecycle may vary. Although deliverables can vary, depending upon project scope, client/project owner requirements, provided items, project characteristics, driving factors, and risk. There are several common process engineering deliverables produced for capital projects, some of the most common deliverables produced within industries such as energy, chemicals, and terminal and logistics are listed below.
- Piping and Instrumentation Diagram (P&ID): A P&ID is a schematic drawing that depicts the configuration of equipment, piping, valving, and instruments used to control and monitor a process facility. The P&ID is the blueprint for the project; it should include all major equipment, piping, and instrumentation. P&IDs are the foundation for maintenance, modifications, and expansions of the processes they visually represent. For this reason, P&IDs are kept “evergreen” and up to date, representing the existing facility.
- Process Flow Diagrams (PFD): A PFD is a simplified schematic that represents a process facility. PFDs typically include icons for equipment such as tanks, pumps, and compressors as well as for their interconnecting fluid streams. The purpose of a PFD is to inform the reader about the equipment present in a plant and allow them to easily comprehend the system’s overall functionality. PFDs tell a story about the material feeds entering a facility, the sequence in which they are processed by different equipment units, and the resulting product streams.
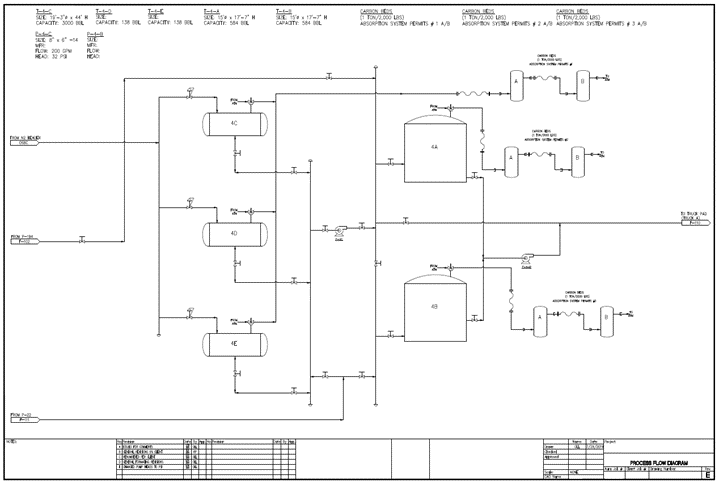
- Heat and Material Balance (H&MB): An H&MB is an essential process engineering deliverable produced by engineers designing or modifying a process facility. The H&MB should include operating conditions and important physical properties of major process streams in the PFD. For each process stream, data such as temperature and pressure, volumetric or mass flow rate, density, viscosity, vapor fraction (if gases are present), and compressibility factor are typically specified. If a process stream has multiple phases, these aspects may be reported for each phase.
- Equipment Data Sheets: Process engineers use simulation tools to develop the information and requirements necessary to source equipment from suppliers. Equipment Data Sheets, sometimes called Process Data Sheets or Mechanical Data Sheets, are used to help specify the requirements for a piece of equipment. During the design process, each piece of equipment shown on a P&ID should have a corresponding data sheet. Process data, such as flow, temperature, pressure, and capacity requirements, are transferred from the PFD and H&MB into the data sheets. Mechanical engineers fill out additional information such as design code, loading information, flange and nozzle requirements, etc. The completed data sheets are used to communicate the technical specifications to the supplier, client, or others who are responsible for approving the design or supplying a conforming quote for the item.
- Instrumentation Data Sheets: Similar to Equipment Data Sheets, process engineers also develop data sheets for instrumentation, such as for pressure transmitters, control valves, etc.
- Pressure Safety Valve (PSV) Study: One of the inherent hazards within the process industries is the handling of toxic and/or flammable fluids that are often under pressure. Excessive pressure could result in the rupture of equipment, resulting in blast damage, fires, or the release of poisonous materials into the environment. PSVs are safety devices designed to protect pressurized vessels or systems during an overpressure event. In this event, PSVs open, allowing the high-pressure material to be safely vented, typically to a flare system. A PSV study typically entails an audit of the sizing of PSVs and their associated piping to ensure the safety of the design.
- Process Simulation: A process simulation is a computer model used by engineers in the design of facilities, such as chemical plants and refineries. Simulation software can predict the behavior of equipment commonly found in process facilities as well as its effects on the materials being processed. For example, an engineer will provide a simulator with known input data, such as equipment design parameters and the connectivity of fluid streams. The simulator then calculates information of interest (e.g. the required power input to a pump). The output from a process simulation may consist of a graphical flowsheet and tabulated thermophysical information about the material and energy streams in the system.
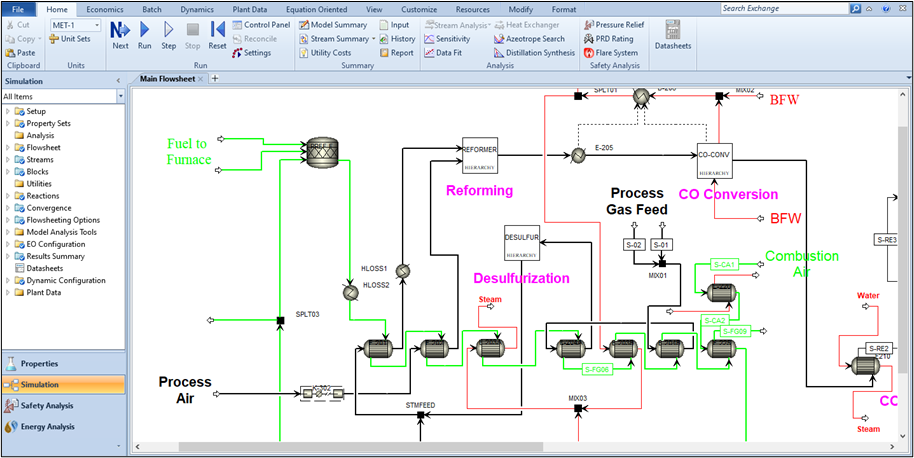
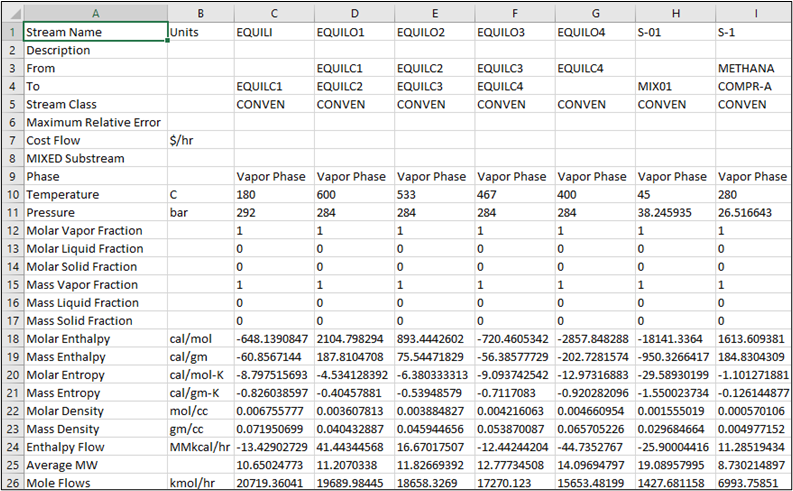
- Hydraulic Study: One unique aspect of process engineering is that it is centered around the handling, processing, and transporting of fluids. Designing a facility to handle or transport fluids poses engineering challenges that are very different from those associated with the transporting of solids. You must understand how to size piping, pumps, and compressors to adequately move fluids from A to B at the desired flow rates. A hydraulic study, in the broadest sense, is a calculation-based analysis to determine whether or not a system can push an adequate amount of fluid through it. Depending on the complexity of the calculation, this study may be done in software as simple as Excel or a process simulation software such as Aspen’s software suite. For example, studies involving a mixture of gases and liquids with dynamic and complex flow patterns would likely be analyzed using simulation software.
Your Capital Project, Your Way
At H+M Industrial EPC, we have more than 30 years of experience providing leading capital project management services to the energy, chemicals, and terminal and logistics industries. Whether your project requires standalone engineering services or an integrated EPC approach, we will work closely with you to drive your project to success—on budget and on time.

The H+M Industrial Team
For over three decades, we have provided best-in-class capital project management services to Energy and Chemical industries through our proven EPC approach. We are dedicated to providing trust, experience, and efficiency through all stages of engineering, procurement, and construction--on budget and on time.
Partnering with H+M Modular
H+M Modular, a division of H+M Industrial EPC, specializes in custom fabricated equipment, modules, and skids for energy and chemical industries. The approach emphasizes the potential for decreased risk through more controlled fabrication, leading to enhanced quality and safety, reduced labor costs and construction times, improved labor availability, and solutions to geographic challenges. We are dedicated to providing trust, experience, and efficiency through all stages of traditional and modular construction projects using our proven EPFC approach, If you're considering modular fabrication, we invite you to connect with us to learn about how modular solutions can improve project outcomes.