Learn about project controls best practices for mitigating risks in capital projects from a leading EPC contractor’s webinar and accompanying guide.
Many risks can occur throughout the capital project life cycle. While some issues are easier to identify and plan for than others, there will be risks that can not be controlled, such as inclement weather. However, with the proper project control best practices and tools, contractors can quickly identify and monitor these risks as soon as possible.
Click here to view the on-demand webinar.
Having work processes and plans in place can help risks from creating further issues as the project progresses. After all, the Construction Industry Institute (CII) performed a study and concluded that “[f]or all projects studied there is over a 90% probability that a project will run over budget.” Keeping in mind that project elements can change throughout execution, it’s easier to mitigate capital project issues when contractors are more accepting of change and willing to quickly adapt plans. A project controls best practice for dealing with inevitable change is to implement a process that is equipped to quantify change and determine a path forward.
Some of the common risks seen across the EPC industry include:
- Poor scope definition/scope creed
- Design errors
- Unexpected site conditions
- Communication/responsibilities
- Issues with scheduling/supply chain alignment
To hear more about identifying risks in capital projects and answers to commonly asked questions, refer to the webinar here.
The bid phase is one of the most crucial elements of the project life cycle. It’s imperative that there is enough time to adequately define the project scope of work and that every party involved is on the same page.
During the bid phase, both the client and contractor should identify any risks and develop a Project Execution Plan (PEP). The PEP will identify the:
- Targeted work schedule
- Critical path of construction
- Amount of manpower
- Highlights of major milestones
Using the PEP to develop a Level 1 schedule and establish a baseline, contractors will be able to identify and recognize deviations.
To hear more about identifying risks during the bid phase of project execution, refer to the webinar here.
Work Breakdown Structure (WBS
A Work Breakdown Structure (WBS) can help contractors assign resources to each activity necessary throughout the project life cycle. Based on discipline, contractors can pull data from the estimate created during the bid phase to complete resource curves. These curves help determine if the schedule created is feasible for the project requirements.
If the schedule created is not feasible, contractors will need to rearrange resources, change deadlines, change logic, and reevaluate durations until they have a resource allocation that's usable. It’s critical to recognize these issues upfront before implementing a schedule because a non-feasible schedule can create many issues such as rework, extra costs, and longer deadlines later in the project life cycle where mitigation is more difficult to achieve.
To view an example of a WBS and to hear more information about how it pertains to schedule management, refer to the webinar here.
Critical Path
Another key component of the execution phase and schedule management is the critical path. A critical path is a sequence of activities, logically linked, which add up to the longest overall duration. This must be identified at the start of the project, as it determines which activities drive project completion. Despite identifying at the beginning of the project, the critical path may change throughout the project life cycle. To identify when/if changes occur, the schedule should be assessed and updated regularly.
To view an example of a critical path and to hear more information about how it pertains to schedule management, refer to the webinar here.
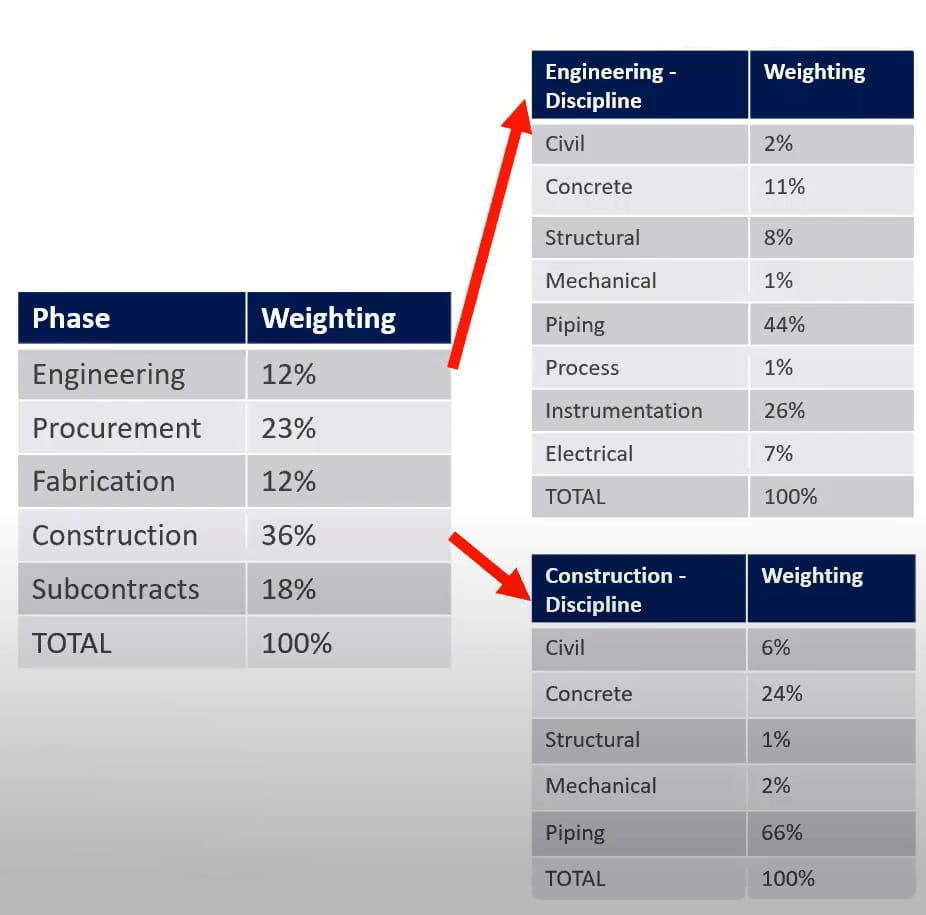
Once the schedule is set up and it’s feasible to start the project, Earned Value Management (EVM) will come into play. Earned Value Management is a method that allows for a project to be measured by the progress achieved. A project controls best practice for Earned Value Management is to have this system in place and establish Rules of Credit for all phases of the project. Rules of Credit are predefined steps with weighting assigned per level of importance that determine the incremental progress per activity.
Once progress has been calculated, project performance can be analyzed using a few elements.
Productivity
A productivity factor is the calculation of earned hours versus actual hours. This is to help determine how contractors are performing compared to how they had planned to perform. If the actual productivity is less than the planned productivity, changes are needed. There can be multiple factors why productivity is lower than planned. A big factor that goes hand-in-hand with productivity is the number of personnel working on the project at a given time.
To view a productivity factor example, refer to the webinar here.
Progress
A progress curve is a straightforward way to see if contractors are meeting their planned progress throughout the planned timeline. This shows the percentage of how much of the project was planned to be finished by a specific date versus the actual percentage of the project finished on those dates. This can also be broken up by disciplines to see which disciplines are ahead of schedule or which ones are not.
To view a progress curve example, refer to the webinar here.
Manpower
Manpower graphs help contractors evaluate the number of personnel and crew members on-site versus the amount needed to meet progress requirements. This is usually shown as a histogram.
To view a manpower histogram example, refer to the webinar here.
To view an example of Rules of Credit in accordance with Earned Value Management and to hear more information about how it pertains to schedule management, refer to the webinar here.
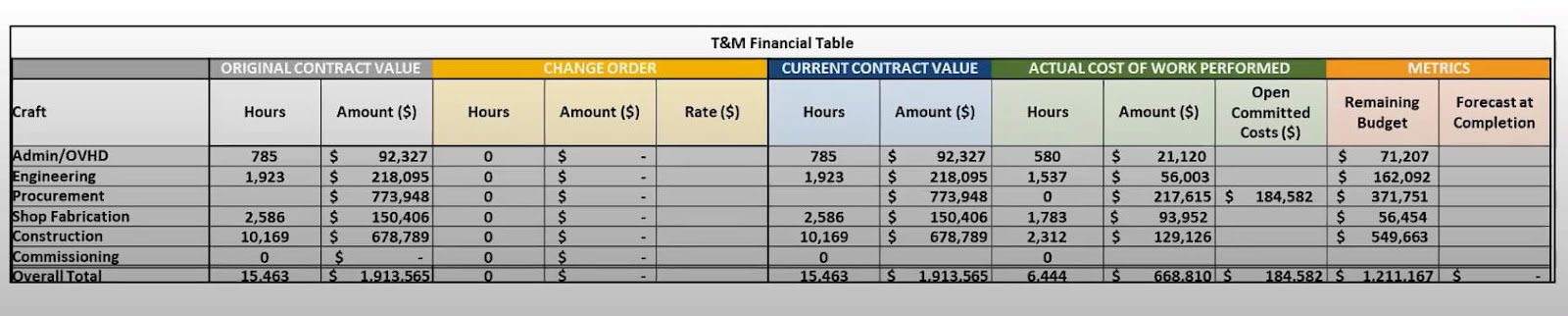
There is a lot of risk associated with cost. Tracking financial performance is important for mitigating such risks. A budget needs to be established and monitored throughout the project to assess how much of the budget is being used in comparison to the projected rates. If the cost is higher than what was projected, it can be forecasted that the project will go over budget. Capturing costs in a change order is an important way to make sure there are no surprises later on.
To view a financial table example, refer to the webinar here.
Any change from the first step of the project through completion should be tracked and documented in a timely manner. This allows for clear communication between client and contractor and prevents unexpected delays or costs from occurring at the end of the project.
Individual changes should be documented using a Change Form that specifies:
- Cost
- Hours
- Scheduled deviation
- Reasoning for change
A project Change Log can be used to summarize all changes and track the status of approval and implementation.
Once a Change Order has been approved, it’s a project controls best practice to integrate all the new information into the project controls tools. These tools include schedule, EVM, and budget.
Schedule
New activities that represent the changes should be added to the schedule and logically tied.
EVM
Line items for all changes should be added to the EVM tracking tool and assigned rules of credit.
Budget
The budget should be updated to include all revised costs and hours.
To learn more about change management, refer to the webinar here.
Project controls best practices show that there should be a standardized report to show key performance indicators (KPIs). This should be issued to both the contractor and the client to have an alignment of information flow. This can include:
- Curves for individual disciplines
- Manpower histograms
- Quantity curves
- Productivity trends
- Cost reports
To view an example of a standardized report, refer to the webinar here.
The next step of a project report is an integrated project controls platform. It is important to integrate all schedule, progress, and cost information together within one system. This allows both internal and external stakeholders to analyze KPIs and provide full transparency on project performance and health.
To learn more about the integrated project controls system, refer to the webinar here.
H+M Industrial EPC: Mitigating Risks in Capital Projects
It’s important to follow project controls best practices to mitigate risks in capital projects. Identifying risks and areas of concern at the start of the project can help prevent issues from happening later down the line. For more than 30 years, H+M Industrial EPC has been a leading contractor in the EPC industry. To stay ahead of project risks, we emphasize mitigation processes and procedures to keep clear lines of communication between clients and internal stakeholders. If you are ready to start your capital project today, contact us now!

The H+M Industrial Team
For over three decades, we have provided best-in-class capital project management services to Energy and Chemical industries through our proven EPC approach. We are dedicated to providing trust, experience, and efficiency through all stages of engineering, procurement, and construction--on budget and on time.
Partnering with H+M Modular
H+M Modular, a division of H+M Industrial EPC, specializes in custom fabricated equipment, modules, and skids for energy and chemical industries. The approach emphasizes the potential for decreased risk through more controlled fabrication, leading to enhanced quality and safety, reduced labor costs and construction times, improved labor availability, and solutions to geographic challenges. We are dedicated to providing trust, experience, and efficiency through all stages of traditional and modular construction projects using our proven EPFC approach, If you're considering modular fabrication, we invite you to connect with us to learn about how modular solutions can improve project outcomes.