During this webinar, Ariel Schrader and Archie Alexander review ways of managing safety risks that have potentially catastrophic consequences in the construction phase of capital projects.
Click here to view the on-demand webinar.
Catastrophic safety events are hazards that have the potential to cause major and life critical injuries. This includes fatalities and permanently debilitating injuries that happen on work sites.
The US Bureau of Labor Statistics reported that in 2018, construction was the highest industry sector for worker fatalities at 19%. This is where managing safety risks in construction comes into play. All instances can be prevented through risk mitigation planning as well as forming safety partnerships between clients and contractors to get ahead of the game when it comes to planning and scheduling.
The hierarchy of controls is a system used in managing safety risks to minimize or eliminate exposure to hazards. This system is represented as an upside down pyramid, with the top of the chart being the most effective to the bottom of the chart being the least effective.
- Elimination (top of the chart): Physically removing the hazard from the workplace (e.g., removing a cord that is a tripping hazard)
- Substitution: Substituting a larger hazard with a smaller hazard (e.g., replacing the use of a Metabo saw with a Portaband saw since it has a slower RPM rotation).
- Engineering Controls: Designing the work to be safer for the employee (e.g., putting kickback protection on a grinder)
- Administrative Controls: Implementing training, procedures, policies, or shift designs that lessen the threat of a hazard (e.g., inspection checklists, rotating workers during lunch, etc.).
- Personal Protective Equipment (PPE) (Bottom of the chart): This is the last line of defense. These are physical elements that are worn by the worker to lessen the damage of a hazard when coming into contact with it (e.g., cut-resistant gloves, safety glasses, etc.)
To learn more about the hierarchy of controls in managing safety risks for construction workers and to take a look at the visual representation of the system, presented by Ariel Schrader, an Associate Safety Professional and HSE Manager at H+M Industrial EPC, watch this part of the webinar!
The ultimate goal of hazard identification is to proactively remove and reduce the possibility that employees are exposed to hazards that have the potential to cause major and life-critical injuries.
To help identify each hazard prior to an incident, extra hazardous work (EHW) is split into different categories based on the scope of the work. By identifying these categories prior to execution, workers will be able to recognize EHW when they come into contact with it and can manage safety risks accordingly for prevention purposes. The EHW categories for EPC projects identified by the H+M Industrial team are as follows:
- Commissioning: This is work related to the startup/shutdown of processes. This includes flushing, impulse blowing, and turning or operating valves.
- Confined Spaces: This is in reference to any work within restricted spaces. Specifically, EHW can occur when performing rescues within confined spaces.
- Demolition: This is work related to the destruction of previous infrastructure. EHW can occur especially when demolishing something with a questionable structural integrity.
- Electrical: This work has a high worker fatality rate in general. This is anything involving powerlines, NCC units, or live electrical equipment.
- Energy Isolation: This is work related to the prevention of the transmission or release of energy (e.g., working on a tie-in). When conducting tie-ins or replacing spools, it’s better to have a physical isolation like a slip line or a blind flange as opposed to a double block and bleed or a block and bleed configuration.
- Environment: This is work that is done within stressful environments such as working in excessive heat or working with asbestos or lead.
- Excavations: This is work related to systematically removing ground to create trenches, cavities, etc. Trenches can collapse, causing fatal injuries to workers.
- Falls: This is work that is done on high platforms or work that requires dangling. This EHW particularly relates to working above water or with water and temporary scaffolding.
- Flammables: In reference to “hot” work, it’s important when welding or grinding on a line that there is no residual product in that line or on that piece of equipment that can cause a flammable atmosphere.
- Lifting: This is work in relation to raising the elevation of the structure. Whether it is a critical lift or tandem lift, each of these will have their own EHW involved.
H+M Industrial EPC has implemented their Extra Hazardous Work program to help with identifying, communicating, and managing safety risks associated with extra hazardous work prior to the job beginning. For information about this program and specific examples of fatalities that have happened in relation to each EHW category, watch this part of the webinar!

Ideally, EHW activities will be identified by either a construction team member or estimating team member during bid walks on-site. The biggest challenge of the EHW project life cycle program is maintaining consistent communication of the program and on different client job sites. Contractors need to be aligned with the job owner’s expectations and vice versa.
Once the EHW is identified, it will be placed into an estimating database where it is mitigated.
The EHW can be mitigated by contractor qualification. In an extreme case, the contractor may need to place it back on the owner's scope of responsibility. In a less extreme case, the contractor may say they can mitigate the EHW but that this aspect of the project will need to be handled by others.
Another way contractors manage safety risks is by mitigation through cost. This can be done by hiring additional management or purchasing specialized PPE.
At the end of the estimating phase, each unique item of hazardous work will be reviewed by company executives and approved.
Having identified EHW, the Engineering team has predetermined items that they will work on. They will also identify additional EHW as they work in detail design. EHW mitigation methods are discussed during constructability reviews.
This is at the stage where the hazardous work plans are finalized and submitted for approval by the corporate office. It is reviewed jointly by both the construction director and the HSE (Health, Safety, and Environment) director and physically signed. Before this happens, a hazardous work plan review meeting is held on-site with construction supervision, HSE supervision, and all crew members. It’s important that everyone is knowledgeable of the plan and the risks
To learn more about the EHW Project Life Cycle at H+M, hear frequently asked questions, and to see a workflow of this life cycle presented by Archie Alexander, the Director of Construction at H+M Industrial EPC, watch this part of the webinar!
Despite the best planning, EHW activities can still be missed during the estimating or engineering phases and can be identified later. Should an EHW activity that was not previously identified arise during the execution of a project, WORK ACTIVITIES MUST STOP until the work is identified, mitigated, approved, and communicated to the workforce.
A Job Safety Analysis (JSA) is the primary process used to identify and mitigate hazards. These are used by crews daily or even multiple times in a day. The forms for a JSA will be filled out with information on the job steps, the corresponding hazards, and how to control the hazard. Every one of these forms are signed off by the directors of HSE and construction.
To learn more about how to deal with unplanned EHW, hear frequently asked questions, and to see a Job Safety Analysis sample presented by Archie Alexander, Director of Construction at H+M Industrial EPC, watch this part of the webinar!
With communication and training, all employees should be mitigating safety risks by preventing last minute judgment calls on-site. This can be done through constructability meetings, model reviews, and kickoff meetings where communication can be encouraged. By including front-line supervisors in the loop of communication, this ensures that team members are receiving their input and having clear direct communication with them. This transparency and communication should also be between contractor and client.
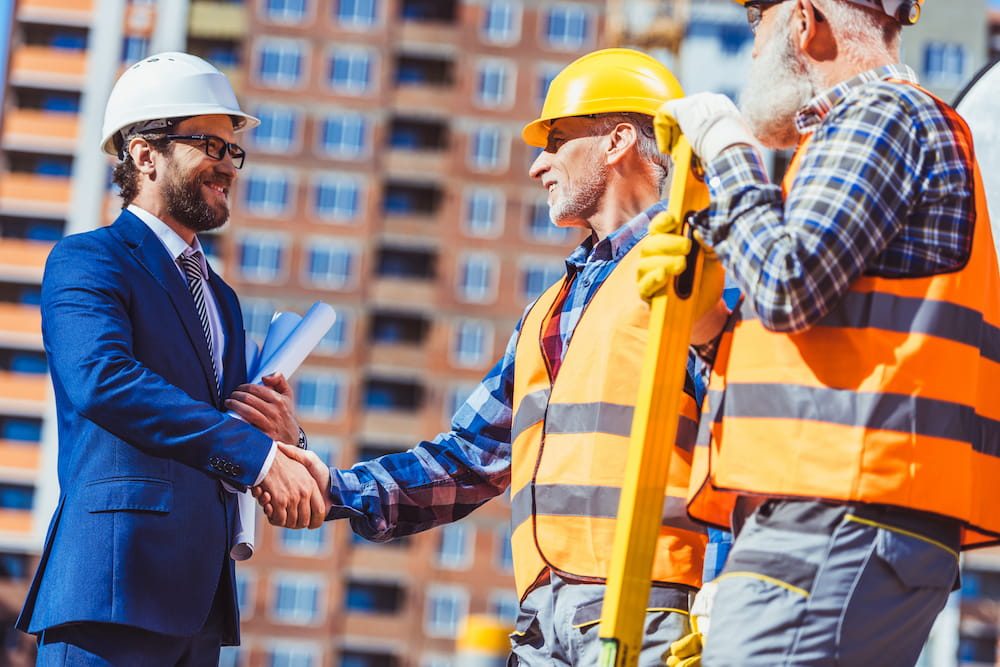
A contractor and client partnership can be achieved through communication and transparency. As a contractor, it’s important to communicate all aspects of the project to the owner to get buy-in and support from management. This will help align expectations around EHW activities, leading to a more cohesive contract where team members work together to improve processes, therefore decreasing risk and increasing the owner’s confidence in their contractor’s competency.
To learn more about managing safety risks in construction for capital projects, watch this part of the webinar to go through an in-depth discussion and view of a case study with extra hazardous work.
For more than 30 years, H+M Industrial EPC has been providing proven EPC services to help benefit and ensure successful capital projects. With awards honoring H+M as “Best in Class” for safety excellence, we live up to the title by continuously improving our safety regulations and procedures to help ensure our workers get through their work day safely and complete capital projects soundly. If you are ready to start your project, contact us today!

The H+M Industrial Team
For over three decades, we have provided best-in-class capital project management services to Energy and Chemical industries through our proven EPC approach. We are dedicated to providing trust, experience, and efficiency through all stages of engineering, procurement, and construction--on budget and on time.
Partnering with H+M Modular
H+M Modular, a division of H+M Industrial EPC, specializes in custom fabricated equipment, modules, and skids for energy and chemical industries. The approach emphasizes the potential for decreased risk through more controlled fabrication, leading to enhanced quality and safety, reduced labor costs and construction times, improved labor availability, and solutions to geographic challenges. We are dedicated to providing trust, experience, and efficiency through all stages of traditional and modular construction projects using our proven EPFC approach, If you're considering modular fabrication, we invite you to connect with us to learn about how modular solutions can improve project outcomes.