In our industry, fabrication is a significant portion of many projects. For each project you are essentially performing the same steps, just to a different set of scopes and requirements. These steps typically involve rebar cutting and bending, structural steel and galvanizing, code vessel work, as well as piping spool and accessory fabrication. Fabrication can also encompass much larger scopes including storage tanks, modules, heat exchanging equipment, process equipment, composite materials, and the list goes on. This work can be done on-site or off-site, both presenting their own set of benefits and challenges.
Implementing the process of off-site fabrication into the daily work can take time and energy that many may not find beneficial, unsure if it is the right decision. There is also a need for an increase in technology in one’s fabrication efforts to make the benefit worthwhile. The key performance indicators for success of pre-fabrication include reduced/improved risk, improved cost, and improved schedule.
Pre-Fabricating for Success
When you decide to pre-fabricate a project, it allows the fabrication work to be performed with ideal material handling environments, while using fabrication and welding equipment which is not economically possible in a field environment. Owner/operators can also ensure less disruption to their site with much of the work being done at their Contractors’ location. Work is performed in a more controlled environment, generally unaffected by weather, mitigating schedule creep. Technology is the reason behind fabrication shops being a more ideal environment. In a shop you can utilize optimal equipment and tools, which increases efficiency, mitigates safety risk, and reduces the cost and duration of the same work performed in the field by approximately 30%.
The table below is a real example of a project analysis I put together with a TIC basis. This analysis was based quantitatively on shop versus field labor unit rates from the Estimator’s Piping Man-Hour Manual, by John S. Page. I did this analysis on a real job to show how much we saved by using shop fabrication instead of fabricating the pipe out in the field. For each scenario, I listed the Pipe Direct Cost, which includes direct shop labor, fringes, overhead, profit, materials, subcontractors, construction equipment, small tools and consumables for shop fabricating the pipe versus fabricating in the field. I also listed the Pipe TIC, which is the same items mentioned before but also factors in all field install scope costs and indirect costs related to the piping for both scenarios. From there you will see the Project TIC, which is the Total Installed Cost, essentially the contract value.
For Pipe Direct Cost alone you can see that there is a cost savings by fabricating in the shop versus in the field, 33% for this example. Then, as you move down the table, you will see some other costs savings that snowball due to things like extended equipment duration and necessary on-site supervision being decreased, along with other indirect costs such as field insurance vs shop insurance. At the end of the table you will see that, for this example, there was a 11.5% savings for shop fabrication when compared to using field fabrication for 100% of the pipe portion. This example shows that you cannot just compare hourly rates. You must evaluate quality, risk, and the methods used to make the most economic choice.
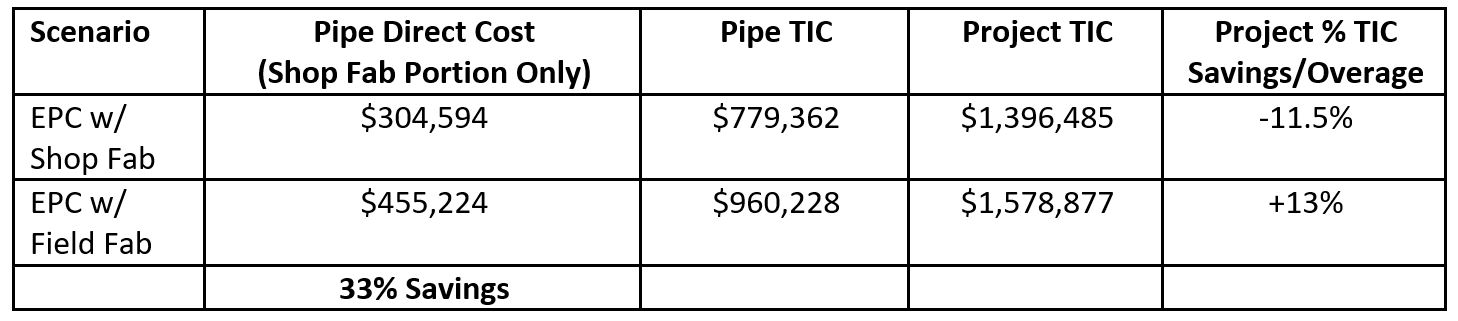
Choosing a contractor with their own fabrication shop is a decision that owners face often. Sometimes they want to contract the work themselves with the intent of a price reduction by managing it themselves. In theory, that sounds like it should work, but has proven time and time again to produce the opposite result. If client’s shop it out there is a greater risk of them losing control and the ability to be agile throughout their project lifecycle. When using a contractor that has their own fabrication shop the entire project team can react more quickly to emergency issues that arise, quick changes that are needed, or any lasts minute elements that need to be added.
Safety. Quality. Accuracy.
Safety, quality, and accuracy are the cornerstones of a successfully executed fabrication project. The improvements associated with the new and improved technologies coming out all help towards each of these goals. It is important for organizations to really dive into what it takes to streamline their fabrication process and determine if the cost / benefit analysis is positive for them. Most of the time, these strategic investments lead to safer environments, increased labor productivity, less people needed to perform the work, mitigation of project risk for Contractor and Client, and an overall improvement in the offered finished product.
To see technology’s true influence on construction labor productivity, the Construction Industry Institute (CII) held a study (CII Study RT-240 - Leveraging Technology to Improve Construction Productivity) to examine how the changes in equipment technology affected labor productivity over 200 construction activities, over a 22-year period. The four factors that were identified to have significant changes were:
1. Amplification of Human Energy
2. Level of Control
3. Functional Range
4. Information Processing
There was previous research on 100 additional activities, over a 27-year period, which focused on examining the relation between changes in construction materials technology and labor productivity. The three primary factors for effective material technology were found to be:
1. Modularization
2. Reduction in unit weight
3. Installation flexibility
With all those factors addressed, the changes in labor productivity was analyzed. The table below shows the significance of technology changes for both groups that CII found statistically significant in terms of labor productivity. “Activities experiencing an improvement in energy, control, functional range, and information processing had at least twice as great of an improvement in labor productivity than activities experiencing no improvement in the technology factors. Likewise, it was found that activities experiencing improvement to modularization, unit weight, and installation encountered at least twice the improvement in labor productivity compared to those activities with no likewise material improvements.” (CII Study RT-240 - Leveraging Technology to Improve Construction Productivity)
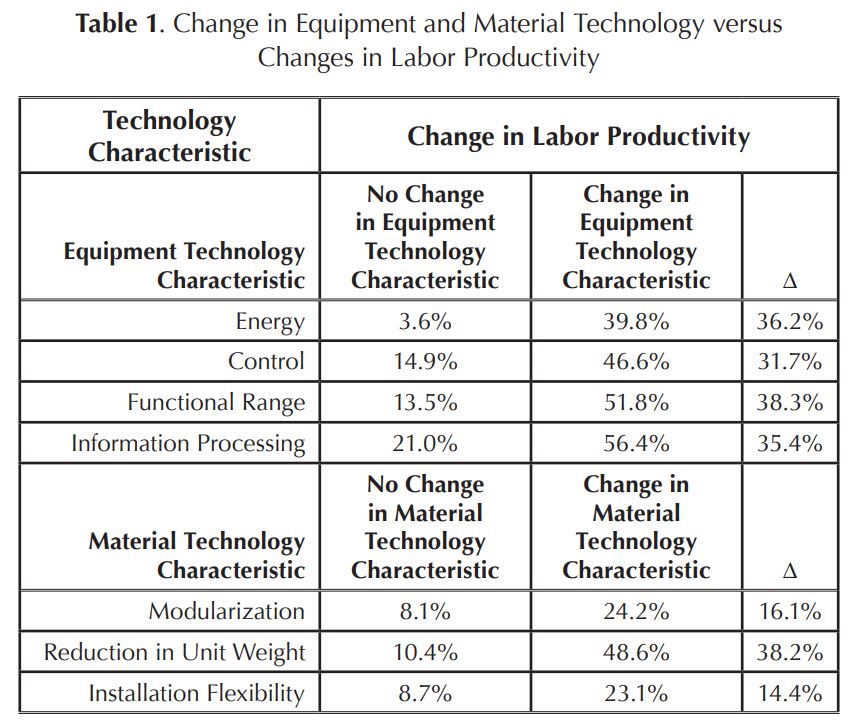
Automation
Specifically, when it comes to technology, automation is one of the most noticeable trends in fabrication right now. Automation has been around for quite some time, however there are specific technologies currently under development with the goal of further improving automation in the genre of piping fabrication. The CII Study RT-183 Design Practices to Facilitate Construction Automation states that "the use of automation in the construction industry has not kept pace with other industries and construction remains a predominantly labor-intensive activity. Cost, availability, and applicability of automated technologies, along with the knowledge and training required to operate the technologies, are obstacles to implementation.” When taken on, these new methods will allow for the work to be done with less people, in a more precise manner that will lead to better quality product and increased safety across the entire crew.
One of our main uses of automation in our own shop include our automated cutting tool. When it comes to productivity, this tool is one of the components that has helped us achieve a 25% increase for our shop over the past year. We can get more done without having to deal with a potential issue of imperfect welds that can arise from non-automated processes.
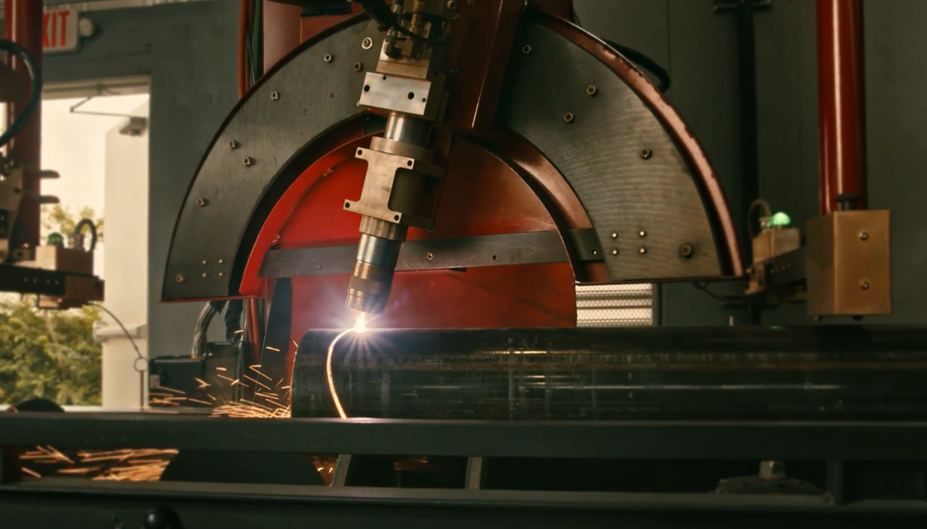
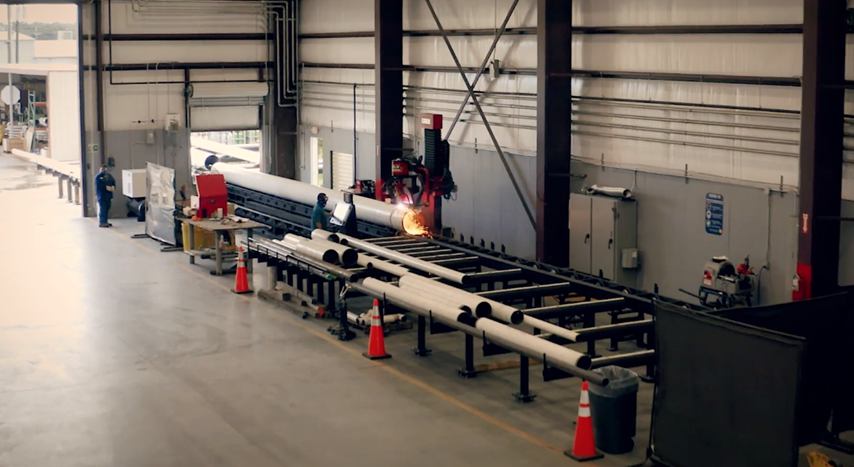
Embracing new technologies and understanding the benefits they offer can sometimes be overshadowed by costs associated with the new equipment or training it will take to get everything up and running. But when viewed as a strategic investment, from an operational or project perspective, the savings really start to add up when considering the long-term benefits. So, take time to see what types of technologies your fabrication shop or preferred vendor has on hand, and see what is being done to improve. Even small, steady changes can lead to vast safety and efficiency improvements.

The H+M Industrial Team
For over three decades, we have provided best-in-class capital project management services to Energy and Chemical industries through our proven EPC approach. We are dedicated to providing trust, experience, and efficiency through all stages of engineering, procurement, and construction--on budget and on time.
Partnering with H+M Modular
H+M Modular, a division of H+M Industrial EPC, specializes in custom fabricated equipment, modules, and skids for energy and chemical industries. The approach emphasizes the potential for decreased risk through more controlled fabrication, leading to enhanced quality and safety, reduced labor costs and construction times, improved labor availability, and solutions to geographic challenges. We are dedicated to providing trust, experience, and efficiency through all stages of traditional and modular construction projects using our proven EPFC approach, If you're considering modular fabrication, we invite you to connect with us to learn about how modular solutions can improve project outcomes.