Manual, labor-intensive jobs such as those in construction run the risk of encountering safety incidents. These incidents can hurt workers, slow progress, and cost contractors the client's trust. Therefore, when selecting contractors for a capital project, it’s important to look for contractors who have preventative measures and incident response plans in place. In order to solidify these processes, contractors need to track various construction safety metrics and prove to clients that safety is an integral component of their culture.
How Should Contractors Track Construction Safety Metrics?
Contractors track incident reports, injury cases, and ‘near misses’ because they can use the data to see trends indicating future injuries and cases that can be prevented with proper mitigation efforts. These mitigations will depend on the cause of the issue and can be as small as a conversation with an individual employee, to something more intensive like implementing company-wide safety protocols with extra training.
Incidents and injuries aren’t the only records that need to be tracked. Contractors that truly place safety first must encourage employees to identify and report at-risk and safe behavior observations and raise awareness of specific activities where hazards proliferate or where safety precautions aren’t being followed properly. For example, at-risk behavior observations reported by on-site employees can point to hazard trends, such as equipment spotter hazards. A spotter is an employee who flags equipment to ensure it doesn’t hit anything. If behavior observations indicate that procedures aren’t being used or followed for spotters, it’s possible that more incidents related to property damages might increase. To prevent these damages from occurring in this example, additional and enhanced spotter training would be beneficial.
Oftentimes, contractors assign dedicated health, safety, and environmental (HSE) supervisors to a project for a part-time or full-time job, depending on the risk level of work and how many people are on site. To ensure proper procedures are utilized, many contractors have the supervisors complete weekly or daily audits. The audit information and data is then organized, tabulated—and over time, analyzed.
To ensure your capital project is in the right hands, before contacting a contractor, ensure they have an excellent support system that invests in their team's safety. This not only benefits their workers and their safety but also benefits your project from possible re-work, delay, or extra expenses.
Necessary Safety Regulations and Measurements To Track
There are certain regulations/measurements that contractors can track to assess their safety benchmarks. Many benefit different parts of the EPC Industry, but the following are the most important and most commonly used metrics.
Experience Modification Rating (EMR)
The experience modification rating (EMR) was established as a benchmark through the contractor's insurance and workers' compensation program. This rate decides how to identify what premiums will be used, but it is also a good measure to see how many kinds of injuries have happened long-term with a specific contractor. Therefore, if a contractor has a high EMR rate, that means they have been paying out a large amount of worker's compensation due to a high rate of injuries.
Note: Recordable injuries must be listed on the OSHA log, but OSHA logs do not capture less severe injuries such as a first aid injury, even if it was severe enough to require some type of compensation to the employee. The EMR can fill the gap and may pick up any other injuries that don't have to be tracked federally. Typically, EMRs under one (1.0) in the EPC industry are deemed acceptable.
Days Away, Restricted or Transferred (DART)
This calculation records the number of incidents resulting in:
- Days Away - When an employee can not work at all.
- Restricted - When the employee can work but only for a short period or can only perform limited duties of their normal job.
- Transfer - When an employee can work but must be transferred to another department, such as from fieldwork to office work.
Lost Time Incident Rate (LTIR)
The LTIR is the lost time on the employee's part as well as the employer’s part. If an employee is hurt, resulting in five days away from work, there are then five days when the contractor will not be paid for their normal job responsibilities. Similar to days away in DART but split to identify the seriousness of each incident. If a contractor has a high LTIR, it means the injuries they are having on-site are pretty severe.
Total Recordable Incident Rate (TRIR)
The total recordable incident rate (TRIR) is an OSHA rate based on a contractor's 300 and 300A logs. The 300 and 300A logs are any injuries that are considered recordable. This calculation is all-encompassing of the DART and LTIR. This records the number of ‘days away from work’ incidents, transferred incidents, and restricted incidents. Additional recordable injuries include hospitalizations, deaths, amputations, loss of an eye, anything beyond first aid treatment, and injuries needing prescription medication. OSHA does not require contractors to have a certain ‘grade’ recorded, but they do require employers with over 10 employees to keep OSHA logs and tracktheir TRIR rate. This is calculated using the equation:
The total number of recordable cases x 200,000 / total hours worked by all employees during the year covered.
Utilize Preventative Measures for Construction Safety
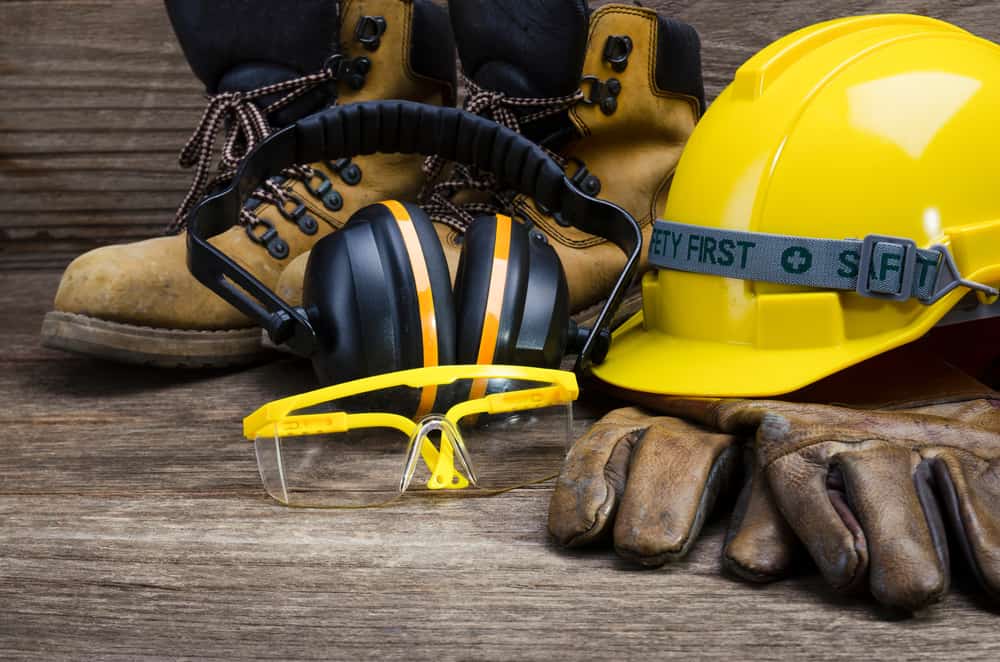
While composing construction safety metrics and KPI (key performance indicators), it is important, keep in mind that this data is intended to create preventative measures for improving procedures as projects continue in the future. The best preventative measures in construction are encouraging workers to report hazards and incidents, ensuring they are adequately trained, and making sure an incident response plan is in place.
Encouraging Workers To Report
The best way to improve construction safety is by applying the data provided by employees on the job to the protocols and procedures of the organization. A large risk is that not all employees will report hazards, minor incidents or ‘near misses.’ Some employees perceive that if they report these, they may get into trouble or have to spend more time filling out incident paperwork than they would like to. This is problematic for contractors because they are unsure what to fix if not told. Giving incentives to employees to report these smaller cases can improve the accuracy of the data and help mitigate future issues.
Ensuring Contractors Train Workers Properly
When selecting a contractor, it’s important that they train their employees properly. Having a thorough training program can point to a safe, well-rounded workforce. Here are a few things to look for in a contractor:
- Before the contractor hires an employee, the employee must match specific requirements and qualifications.
- Employees receive OSHA compliance training, PPE training, and chemical training.
- They conducted both theoretical and physical performance evaluations of employee skill sets and knowledge of the employees' specific craft (if required).
- They train employees with regard to client requirements.
- Their onboarding process has a clear-cut program with regular evaluations.
Ensure an Incident Response Plan Is in Place
The majority of construction safety metrics and KPI are utilized for preventative maintenance, but it is still important to put in place an incident response plan for what to do after an incident does occur. These could include, but are not limited to:
- If someone is injured, ensure the priority is providing them with care.
- Create notifications for clients, managers, safety directors, and others to keep everyone up-to-date.
- Secure the site. It is important to leave as much of the scene as it was in case of an investigation while also removing other employees from that area to prevent further injuries.
- Collect witness statements from those directly impacted or witnessed the incident. It’s important that these statements align. If they do not align, communicate with the injured party to investigate discrepancies.
- Collect any documents or procedures that were used. For example, the filled out Job Safety Analysis (JSA) or work permit.
- Ensure employees have reviewed their procedures properly and provide training when necessary.
- If the employees behavior indicates concern, perform a drug and alcohol test to rule out any impairments.
- Go forward with the formal investigation
- Put together a timeline of events for the safety department and HSE supervisors for a root cause analysis (RCA).
H+M Industrial: Making Safety a Lifestyle
H+M Industrial EPC has created the “Good Catch” program to incentivize employees in a variety of ways to report their near misses. The program gives employees a positive connotation regarding reporting. The H+M HSE Department created a streamline approach to the program so that employees no longer have to fill out lengthy paperwork or be apprehensive about reporting the incident.

The H+M Industrial Team
For over three decades, we have provided best-in-class capital project management services to Energy and Chemical industries through our proven EPC approach. We are dedicated to providing trust, experience, and efficiency through all stages of engineering, procurement, and construction--on budget and on time.
Partnering with H+M Modular
H+M Modular, a division of H+M Industrial EPC, specializes in custom fabricated equipment, modules, and skids for energy and chemical industries. The approach emphasizes the potential for decreased risk through more controlled fabrication, leading to enhanced quality and safety, reduced labor costs and construction times, improved labor availability, and solutions to geographic challenges. We are dedicated to providing trust, experience, and efficiency through all stages of traditional and modular construction projects using our proven EPFC approach, If you're considering modular fabrication, we invite you to connect with us to learn about how modular solutions can improve project outcomes.