This webinar is ideal for professionals involved in all phases of capital project execution.
Using laser scanning in construction can help with constructability for the project. When utilized, projects can potentially see lessened rework and have more opportunities for improvement when applied in the front end of the project rather than later in the project phases. This webinar and blog focus on how using laser scanning in construction can specifically benefit constructability purposes throughout each phase of the project life cycle.
Click here to view the webinar.
To skip around the blog, use our index:
Constructability is a method to mitigate project risk and produce the most efficient installation that will minimize a project’s schedule and cost. Constructability should be evaluated for every project stage, beginning with Scope Development during FEL 1. This can be accomplished by having meetings throughout the project phases and fostering communication to benefit teamwork. One of the ways to incorporate constructability in capital projects is by using laser scanning.
Note: To improve constructability even more, constructability reviews can be provided early in the project life cycle to identify extra ways to minimize rework, schedule changes, and cost overruns throughout the project phases.
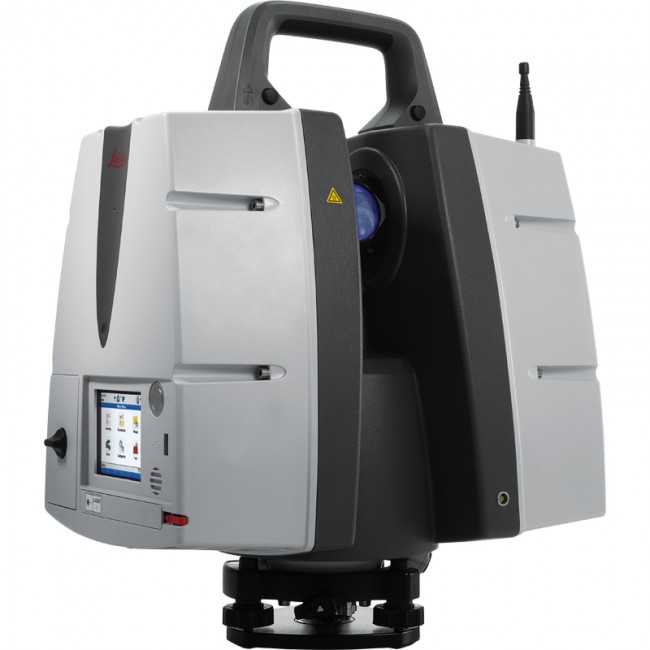
3D laser scanning uses lasers to digitally capture the shape of a 3D object. The data is recorded to a point cloud system which can then be registered to a coordinate system and loaded into various design software for use. Laser scanning allows engineering teams to capture existing infrastructure inside industry complexes.
Laser scanning outperforms conventional methods of recording data points. Using laser scanning in construction instead of manual measurement pulling is oftentimes safer and more accurate. Contractors are now able to reach areas and collect measurements that a person may have struggled to get to safely without this technology. Engineers and construction personnel can use this data to help mitigate significant project risks.
By using laser scanning in construction projects, contractors can thoroughly improve constructability throughout the project life cycle. The various disciplines involved in capital projects can use the 3D laser scan for different purposes in different project phases. By identifying each project life cycle and the benefits of 3D laser scanning, this article and webinar hopes to show how constructability can improve when using laser scanning in construction.
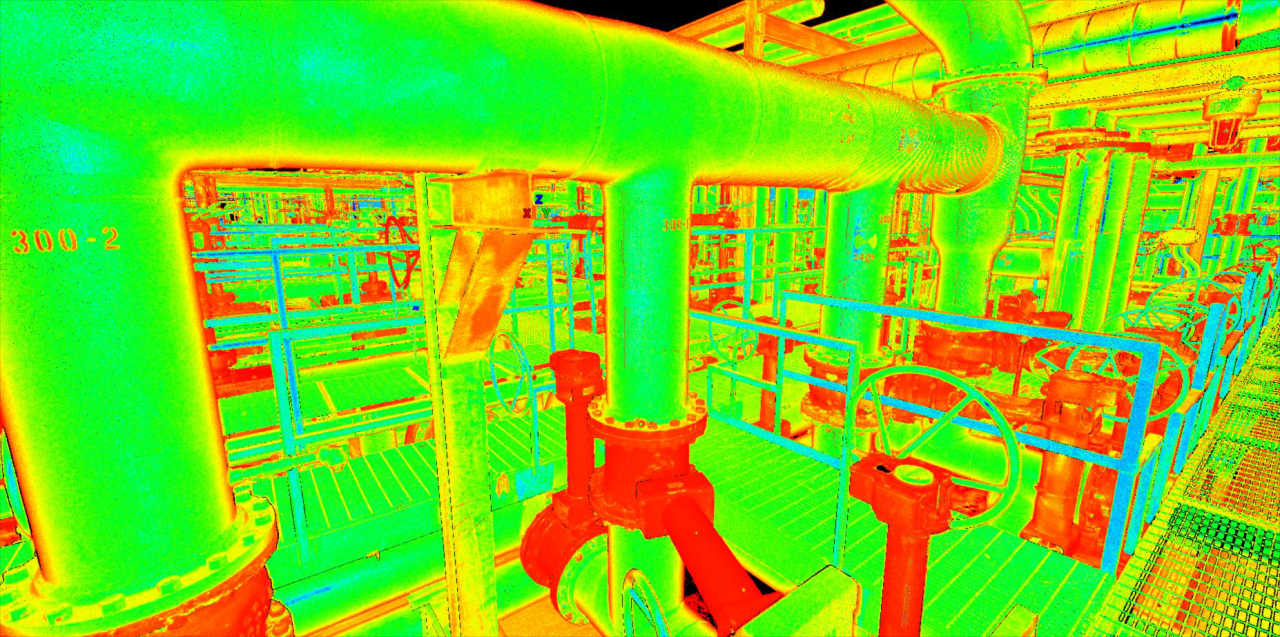
Within the scope development phase, the primary objective is to nail down the scope. Having this as developed as possible benefits all future phases.To complete this objective, engineers will need as many details as possible about the upcoming project.
3D laser scanning provides engineers a virtual walkthrough of the existing site to:
- Identify various layouts
- Identify tie-ins
- Discuss future projects/maintenance
- Locate access areas
- Identify turnaround times
If a site has limited access, engineers can identify necessary information about the site without having to visit the facility. With access to a model of the site, more people can take a look at the information themselves to identify the scope of work rather than relying on a single person or group of individuals to collect the information. This improves communication and teamwork by providing engineers with a source of information to cite from.
Project Example:
Suppose a group of engineers is trying to find the best location for new equipment with minimal impact on existing infrastructure. 3D laser scanning can scan the facility and provide a model to determine where the best fit is with the least impact on operations, maintenance, construction, and future work in the areas. For more information on this example, refer to the webinar here.
The detailed design and engineering phase is the last phase of engineering after all parameters of scope have been defined. This phase's primary objective is to produce the optimal design for project success. To improve constructability within this project phase, the 3D laser scan can be loaded into design software to provide a high level of accuracy in identifying new design overlaps with old infrastructure.
By using laser scanning in construction, engineers can use the model to test designs, plan around obstructions, remove inaccuracies, and decrease the amount of time engineers need to spend in the field. The turnaround time for the engineering and design phase has the potential to be completed more quickly when using a laser scanner. Operation maintenance crews can also visualize the designs in real time rather than viewing the new infrastructure designs separately from the old infrastructure.
Project Example 1:
Suppose a group of engineers is looking to design around an existing facility while avoiding clashes. By overlaying the new model onto the existing model, they can identify any concerns with clashes, operations, maintenance, and more. For more information on this example, refer to the webinar here.
Project Example 2:
Suppose a new design is clashing with existing steel and tie-ins on an existing facility. After viewing the scan, engineers can make the appropriate decision to mitigate and modify the existing design or mitigate and modify the new design. For more information on this example, refer to the webinar here.
Project Example 3:
Suppose a group of engineers are looking to locate the tie-ins and identify the demo scope of an existing facility. By using laser scanning in construction, these engineers can take photos to provide to the field for better identification purposes. For more information on this example, refer to the webinar here.
At this point in the project life cycle, the facility has been scanned, and the new design has been modeled and likely reviewed multiple times. The most effective way of using laser scanning in construction for constructability in this phase is to verify critical items of fabrication such as:
- Field erected tanks
- Shop fab vessels
- Equipment with higher design tolerances
- Unique pipe geometry
By scanning a critical item and virtually placing the item into the model, engineers can identify alignments and the level of accuracy for implementation. Having this information prior to the equipment arriving on site allows contractors to make adjustments before implementation to help ensure a swift and seamless installation process.
Project Example 1:
Suppose the vessel is FRP, which allows for higher tolerances, and the vessel dictated the scope due to the large bore lines. By scanning the vessel in the fabrication shop, engineers can drop it into the model to identify if any changes need to be made before sending it off to the field for installation. For more information on this example, refer to the webinar here.
Project Example 2:
Suppose the tank was field erected, and upon completion of the tank, engineers found that the nozzle angle and projects were slightly off from the drawing/model. This causes a critical issue because the pipe is lined to go to the tank. To fix this issue, engineers can scan the tank at the site and drop it into the model to identify any discrepancies and figure out a solution prior to install. For more information on this example, refer to the webinar here.
In the construction phase, it’s important that the critical information and risks have already been assessed. Despite previous planning efforts, installation of equipment can potentially come with issues; fortunately, if a clash does happen during the construction phase, workers can view the project and problem on the scan to ensure it does not create another issue.
Project Example 1:
Suppose there is a design discrepancy between discipline packages—a support pipe was installed incorrectly by an outside organization. By assessing the scan, the pipe can be modified due to the clash to ensure critical pieces are secured. For more information on this example, refer to the webinar here.
Project Example 2:
Suppose an 18” weld at north/upper 45 was sitting on a new pipe support. By assessing the scan, the decision was made to lengthen the header, and pushing the north/upper 45 further south/down will bring it off the pipe support. This fix flushed the 45 south, but the travel had to be shortened to keep the piping on the new pipe support. The 6” line also had to be modified for the same reason. For more information on this example, refer to the webinar here.
Going through the project life cycle, by using laser scanning in construction for constructability purposes, contractors can improve the overall outcome of the project. At H+M Industrial EPC, our 3D laser scanning services provide unique advantages and greater efficiency through each phase of your project, from front-end planning to construction. With over 30 years of experience and awards recognizing our dedication to safety, improving constructability for capital projects is one of H+M’s top priorities to help ensure the success of your completed project. Ready to start your project? Reach out today!

The H+M Industrial Team
For over three decades, we have provided best-in-class capital project management services to Energy and Chemical industries through our proven EPC approach. We are dedicated to providing trust, experience, and efficiency through all stages of engineering, procurement, and construction--on budget and on time.
Partnering with H+M Modular
H+M Modular, a division of H+M Industrial EPC, specializes in custom fabricated equipment, modules, and skids for energy and chemical industries. The approach emphasizes the potential for decreased risk through more controlled fabrication, leading to enhanced quality and safety, reduced labor costs and construction times, improved labor availability, and solutions to geographic challenges. We are dedicated to providing trust, experience, and efficiency through all stages of traditional and modular construction projects using our proven EPFC approach, If you're considering modular fabrication, we invite you to connect with us to learn about how modular solutions can improve project outcomes.