Design-build, similar to turnkey and EPC, is a common method used for industrial capital projects due to the consistent and cohesive nature of the approach. Design-build allows for superior communication and reduced misunderstandings as a single team works to accomplish the project from scope development to construction.
This method is gaining traction in the construction industry for all project sizes, as it offers many benefits to the owner or agency of the project as compared to traditional project delivery methods.
While design-build project stages can be categorized in several ways, a common layout is as follows:
To understand what a design-build contract is, let’s look at the benefits and what each stage entails.
What Is a Design-Build Contract? (The Basics)
Design-build is a method of capital project delivery in which one design-build company works under a single contract with a project owner, providing all design and construction services. One team completes the project under one contract, providing a cohesive flow of work from engineering to completion.
Industrial design-build contracts may be used for projects within industries such as chemical, terminal and logistics, and energy.
Design-Build vs. Design-Bid-Build
In a typical design-bid-build project, the owner outlines the scope of the project before bidding detail design. The result of detail design is an IFC (Issued for Construction) package used to bid construction. At this point, the general contractor, subcontractors, and material suppliers or vendors carry out the build per the design specifications.
Scheduling and budget issues may present in the construction phase of design-bid-build projects, as each of the niche groups tends to remain siloed. This technique often results in a prolonged timeline, as time must be taken for bidding processes for both design and construction, followed by a lengthy contracting and negotiation process.
The design-build method is more of a one-stop shop in which the owner delegates all responsibilities to the design-build company. The design-build method of delivery can often be significantly more efficient in terms of the overall timeline of a project, among other benefits.
Owner/Agency Benefits for Design-Build Contracts
- Price certainty and reduced financial unknowns: As opposed to design-bid-build project delivery methods, project owners know the fixed price upfront, ensuring total cost for all stages. This allows project owners to calculate ROI and reduce project risk properly.
- Reduced issues around change management: Design-build approaches greatly reduce change management challenges and change orders that may occur in traditional approaches due to a lack of cohesion between the separate design and construction companies involved. Errors and omissions in design lead to construction change orders.
- Faster project delivery: Work can be completed faster and sooner due to the elimination of the transactional nature of traditional methods and the ability to overlap various project stages.
- Potential total cost savings: While the individual bids of “traditional” project execution may sum to less, frequently, the “total cost” is more when considering time, change, and increased risk. Integrated, collaborative teams support higher efficiency work.
- Consistent quality: Design-build companies aim to meet performance and quality needs versus minimum design requirements and set standards that must extend through all phases of the project.
- Singular responsibility: The design-build company is accountable for the schedule, cost, and results.
- Reduced litigation claims: Project owners can reduce claims by closing warranty gaps.
- Reduced administrative needs: Without the need to manage numerous contracts, owners can place more focus on the project.
Design-Build Contract Project Stages
To fully provide clarity and a full answer to the question, “What is a design-build contract?” let’s walk through the five stages—front-end planning; design-build company selection; engineering and design; fabrication, procurement, and construction; and commissioning and startup.
Front-end planning can occur before or after the design-build company selection. Incorporating front-end planning after the company selection allows for continuity through design and construction planning. During this stage, the design-build company analyzes and evaluates the overall constructability and establishes the scope of the project.
Contractors, engineers, and other consultants work together to assess existing structures and establish what must be done before construction begins. Work packaging will be defined during this stage to evaluate the process at the front end.
The contract can be reviewed, negotiated, and signed following scope development. This contract will include the project's total cost from design to construction and may be in the form of a fixed price or time-and-materials contract. However, the contract type is dependent on the design-build company and what is best for individual projects.
In this stage, project owners carefully vet potential candidates from design-build companies. Company selection is critical for the success of the project, and the company that best understands the design-build process, as well as the project owner’s vision, needs, and budget, should be selected.
The company should also have construction capabilities in-house, as this is not always a given. Many design-build companies subcontract with a separate construction company, which can lead to inconsistencies between design and construction.
Once project scope parameters, such as timeline, site, and budget, have been clearly defined, engineering and design begin. In this stage, all project team members work together to develop the optimal design for the project’s success to maintain a balance between efficiency and budget. The end product from this phase is a set of highly disciplined drawings that will be used for construction.
Initial construction may begin during the design phase to speed up the process. With careful planning by design-build companies, the construction of various components of the project can occur while other working packages are still in the engineering/design or fabrication stage. Regardless, during this stage, all parties collaborate and work together to meet predetermined goals and dates per the scope of the project.
After the project has been completed, the design-build company provides a detailed overview of the project as a whole. Since all the work is executed by a single entity, the post-construction stage is often much more streamlined than the traditional delivery method. Commissioning and startup are often, but not always, included in design-build projects.
H+M Industrial EPC | Local Capital Project Expertise
The design-build approach can provide significant benefits to project owners in terms of cost, schedule, and overall quality. However, careful consideration is required when vetting potential design-build companies to carry out your project. It is critical that the company has extensive experience with the design-build process and has full in-house expertise and capability for all stages of the project.
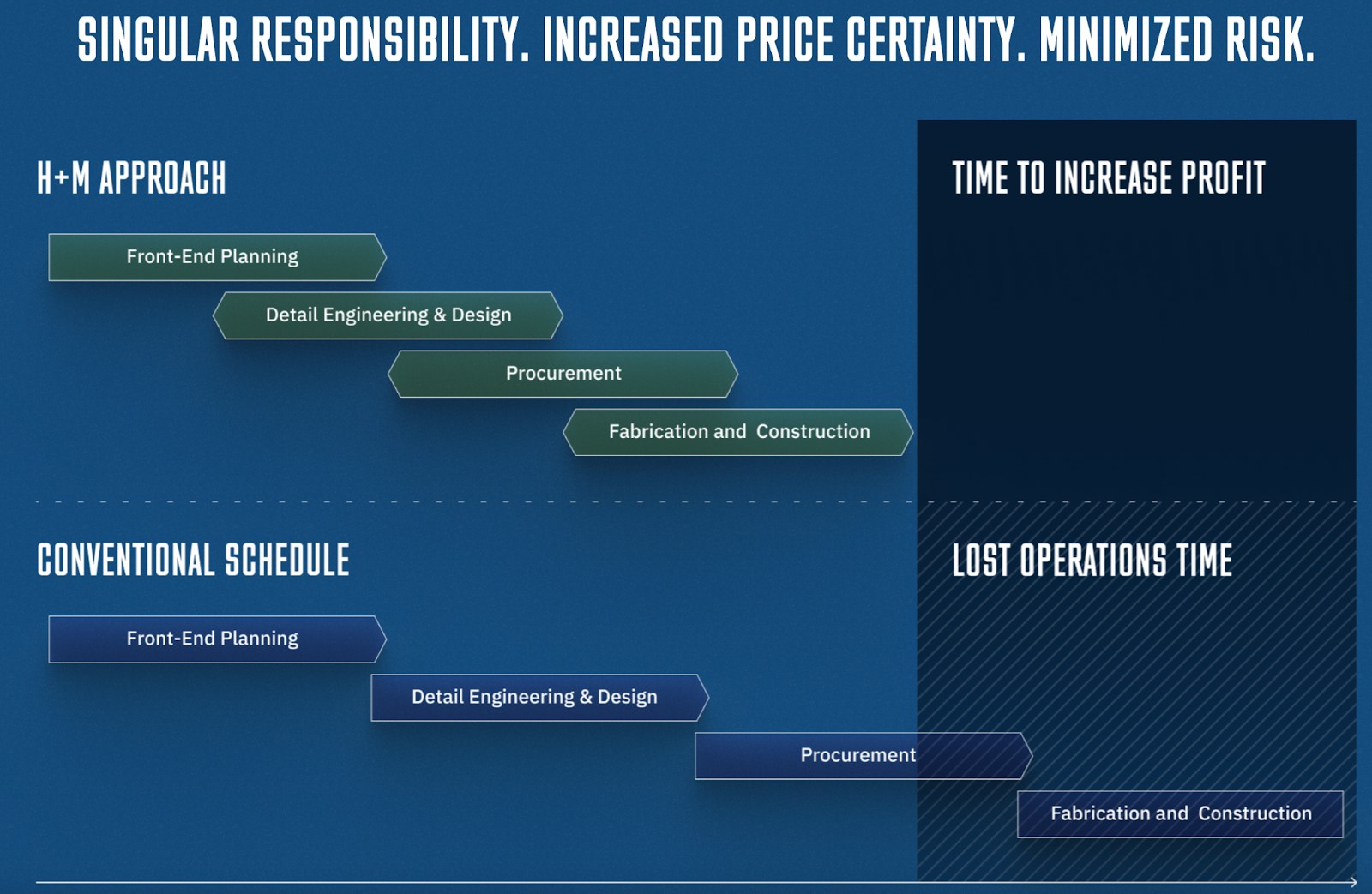
If you still have questions surrounding “What is a design-build contract,” we can help.
For more than 35 years, H+M Industrial EPC has successfully provided top-notch capital project management services to energy, chemical, and terminal and logistics industries through a proven EPC approach. As your project execution expert, we will collaborate with you to complete your project on budget and on time.
With the internal execution of all project steps, our strategic EPC approach provides supply chain certainty, reducing the owner’s cost and keeping project lifecycles intact.
Want to Learn More About Project Management?
Download “The Top 10 Things To Look Out For When Examining Your Design-Build Contract”
.jpg)

The H+M Industrial Team
For over three decades, we have provided best-in-class capital project management services to Energy and Chemical industries through our proven EPC approach. We are dedicated to providing trust, experience, and efficiency through all stages of engineering, procurement, and construction--on budget and on time.
Partnering with H+M Modular
H+M Modular, a division of H+M Industrial EPC, specializes in custom fabricated equipment, modules, and skids for energy and chemical industries. The approach emphasizes the potential for decreased risk through more controlled fabrication, leading to enhanced quality and safety, reduced labor costs and construction times, improved labor availability, and solutions to geographic challenges. We are dedicated to providing trust, experience, and efficiency through all stages of traditional and modular construction projects using our proven EPFC approach, If you're considering modular fabrication, we invite you to connect with us to learn about how modular solutions can improve project outcomes.