When construction projects fail, it is often due to conflicts or circumstances that cause schedule delays and cost overruns. For many capital projects, cost and schedule are not just driving factors, they are metrics that indicate project success/project failure. Capital projects are complex and have many moving parts that can introduce risk and uncertainty, ultimately impacting project performance and success.
As of 2022, more than 50% of construction project owners have experienced at least one underperforming project worldwide (61% in the U.S.), despite confidence in planning and project controls. Project owners also reported that only 31% of their projects were delivered within 10% of the budget, with 25% of their projects delivered within 10% of the original project schedule.
To paint a more detailed picture of why construction projects fail, we have provided a list of four common causes of project failure, in addition to insights on how to improve project outcomes through improved communication, alignment, and collaboration.
Why Do Construction Projects Fail?
Below are four common reasons why construction projects fail:
- Gaps in communication and/or alignment: Frequent and effective communication is vital to the success of any capital project. Insufficient communication and a lack of alignment between the contractor, the contractor’s team, and stakeholders can cause a myriad of problems throughout a capital project’s life cycle. Poor alignment or collaboration, particularly during early project phases, can have a domino effect and can greatly impact project performance and success. When project team members or stakeholders are not receiving the correct information at all times, the consequences can be large—and costly.
- Late or insufficient planning: At the end of the day, poor project planning results in poor project execution. Tight, inflexible schedules are very common in construction projects. More often than not, the more effort put into project planning, the greater the ability to meet project goals, deadlines, and financial constraints.
- Change orders: Even with strong attention to detail, proper planning, and a robust scope definition, project changes are always possible, particularly when you come across unforeseen circumstances, such as unexpected site conditions (ranging from environmental and infrastructure problems to uncharted utilities and “unknowns” such as underground piping), weather, and supply chain issues. Numerous change orders or poor change management work processes introduce risk and can greatly impact project success regarding timeline and budget. Change management involves change identification, planning, evaluation, and implementation and therefore should be emphasized throughout the entire project life cycle, from front-end planning through construction.
- Scope creep: Scope creep refers to the process in which the amount of work grows beyond the original agreement. It is important to control the scope and to not allow new project “desires” to creep in. Changes in scope definition require new resources, materials, and staff as well as schedule changes/delays and additional funding.
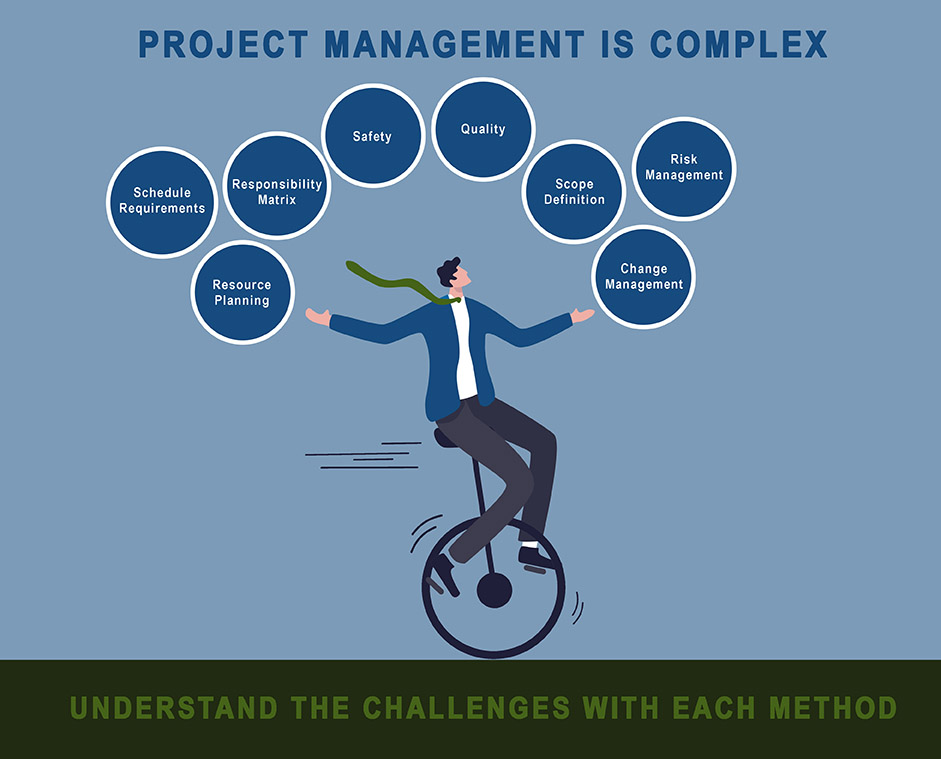
Improving Project Outcomes Through Improved Communication and Alignment
While communication is a crucial element in any industry, it is particularly important in the construction industry. Best practices for project team communication and alignment are detailed below:
- Define the rules of engagement. Rules of engagement may include how often the project owner expects updates and project reports, what channel(s) of communication should be utilized, and the main point of contact. Consistent and frequent communication can allow contractors to continue ensuring alignment between all parties throughout the project life cycle.
- Ensure early stakeholder and team alignment during the front-end planning phase.
- Involve all disciplines and functions in early project stages to gain contractor team alignment. The involvement of construction personnel early in the project life cycle can ensure designs promote construction feasibility and efficiency in addition to future site maintainability.
- Incorporate robust project controls. Utilizing an integrated location, such as a portal or dashboard, to communicate and view all project data and information provides all parties with the real-time data that is crucial to make rapid, yet informed, decisions.
H+M: Ensuring Capital Project Success for More Than 30 Years
At H+M Industrial EPC, we have more than 30 years of experience providing leading capital project management services to the energy, chemical, and terminal and logistics industries. Whether your project requires a design-build or a design-bid-build approach, we will work closely with you to drive your project to success—on budget and on time.

The H+M Industrial Team
For over three decades, we have provided best-in-class capital project management services to Energy and Chemical industries through our proven EPC approach. We are dedicated to providing trust, experience, and efficiency through all stages of engineering, procurement, and construction--on budget and on time.
Partnering with H+M Modular
H+M Modular, a division of H+M Industrial EPC, specializes in custom fabricated equipment, modules, and skids for energy and chemical industries. The approach emphasizes the potential for decreased risk through more controlled fabrication, leading to enhanced quality and safety, reduced labor costs and construction times, improved labor availability, and solutions to geographic challenges. We are dedicated to providing trust, experience, and efficiency through all stages of traditional and modular construction projects using our proven EPFC approach, If you're considering modular fabrication, we invite you to connect with us to learn about how modular solutions can improve project outcomes.